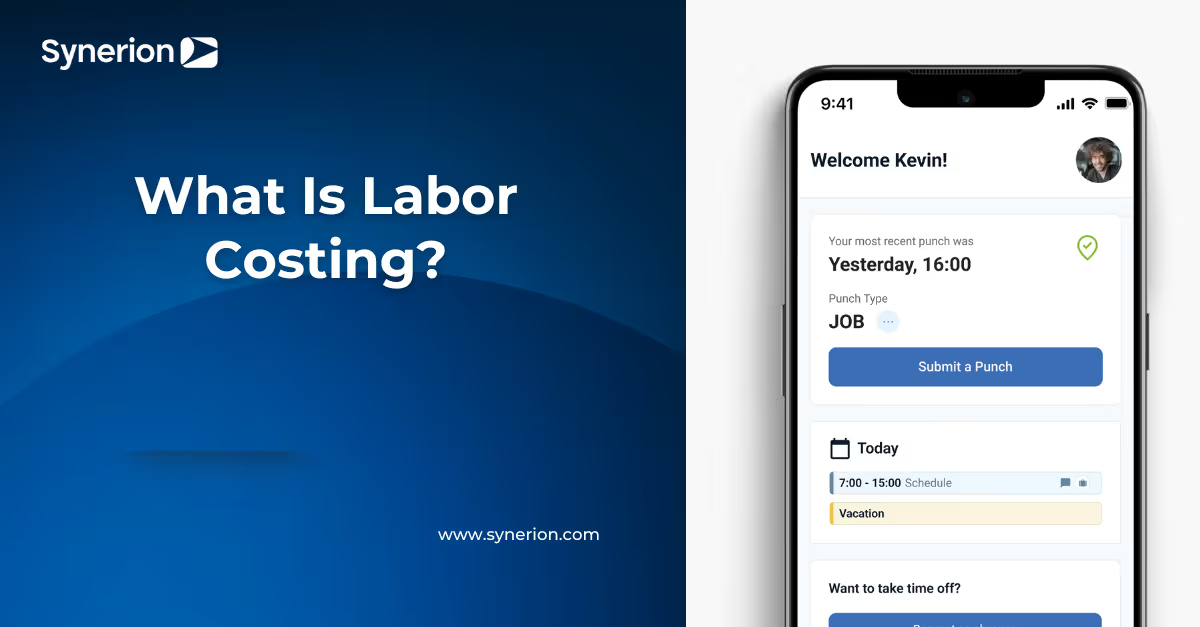
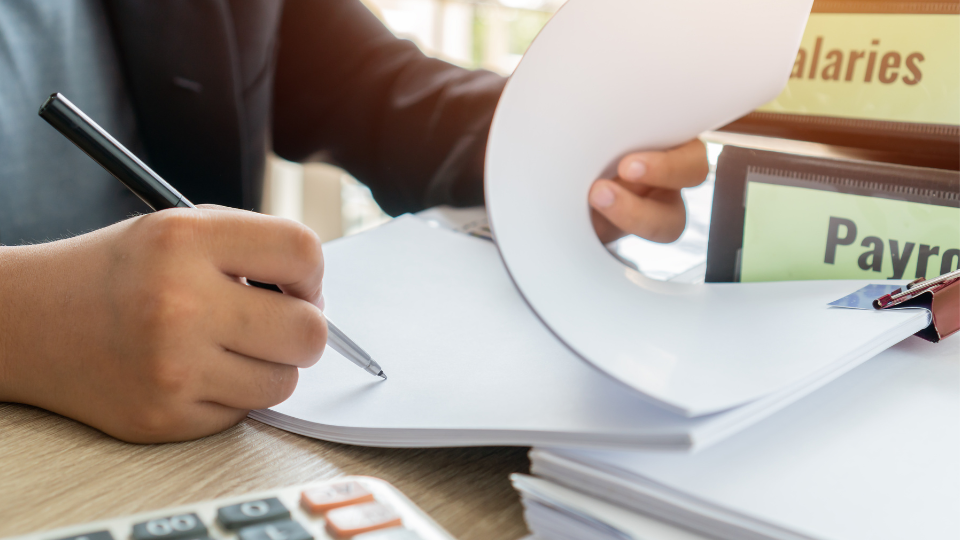
What Is Labor Costing? How To Calculate And Key Examples
Many business owners believe they have a clear handle on labor costs, but in reality, those numbers are often miscalculated. Hidden discrepancies between estimated and actual expenses can quietly eat into profits, making it harder to manage budgets effectively and plan for growth.
Labor costing reveals what's happening with your biggest expense category. When you understand the complete picture of what each employee costs your business, you gain the power to make smarter pricing decisions and identify profit opportunities others miss.
Main Takeaways:
- Labor costing goes beyond wages; it includes taxes, benefits, and hidden expenses that can add 25–40% to your base payroll
- Understanding direct and indirect costs helps you track profitability by product, service, or department
- Fixed and variable costs affect labor budgeting differently—fixed costs like salaries and benefits remain stable, while variable costs such as overtime and seasonal labor rise and fall with demand
- Calculating total labor cost requires factoring in wages, payroll taxes, benefits, and other employer contributions
- Using workforce management tools like Synerion can streamline labor tracking, improve cost visibility, and reduce unnecessary overtime
What Is Labor Costing?
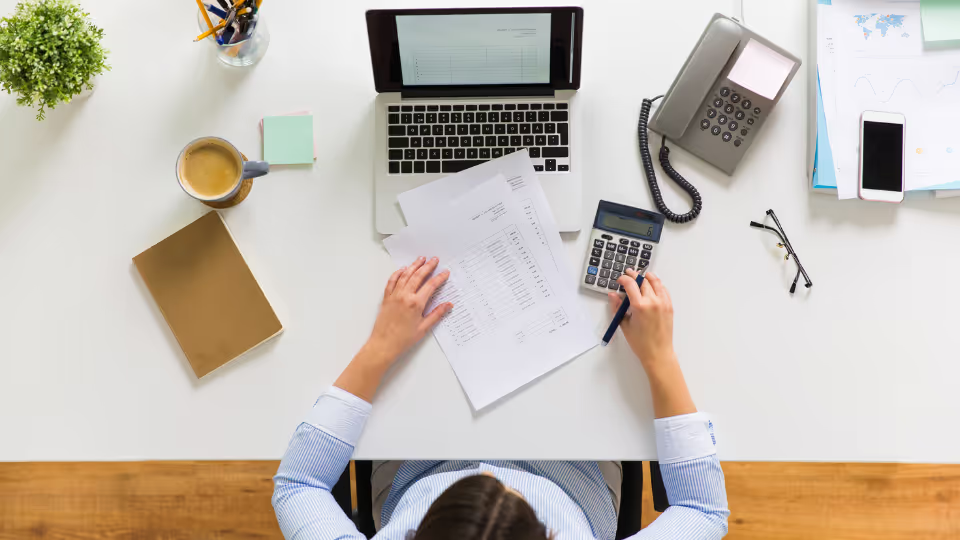
Labor costing is the process of identifying, measuring, and allocating all expenses related to employing workers in your business. The cost of labor includes wages, taxes, benefits, and other hidden expenses that impact your bottom line. Understanding what labor costs are helps you make informed decisions about pricing, budgeting, and resource allocation.
Unlike simple payroll calculations, comprehensive labor costing captures both direct payments and supplementary costs. These additional expenses can add significantly to base wage expenses, making them crucial for accurate financial planning.
Direct vs. Indirect Costs
Direct labor costs are expenses tied specifically to producing goods or delivering services. These include wages paid to production workers and others directly involved in creating your product.
Indirect labor costs support operations but aren't directly tied to production. These include supervisory salaries, administrative staff, and maintenance personnel.
Quick Cost Identification
When determining direct vs. indirect costs, ask: "Would this labor expense exist if we stopped making a specific product?" If yes, it's likely direct. If it continues regardless, it's probably indirect.
Examples of each type:
- Direct costs: Production worker wages, service technician pay, piece-rate payments
- Indirect costs: Management salaries, quality control personnel, HR staff
Why Labor Costing Matters
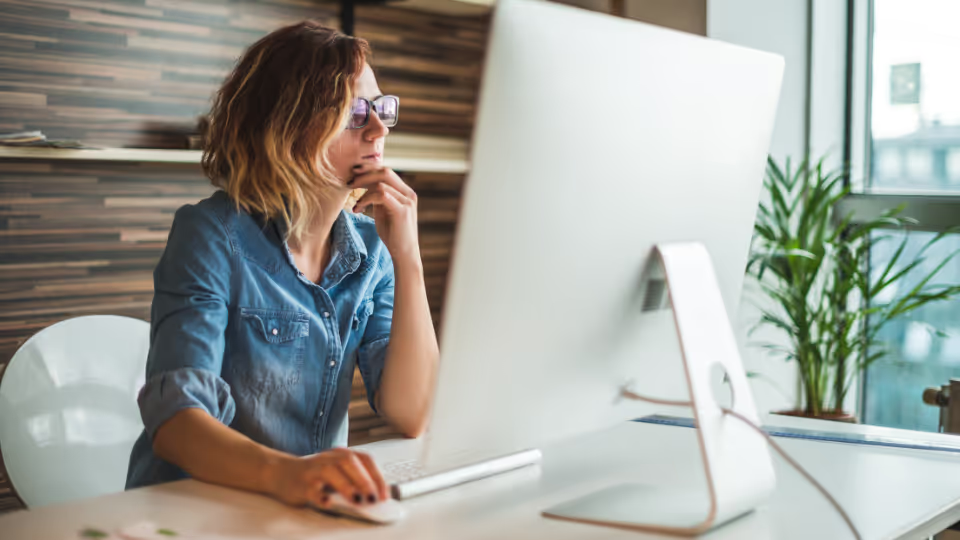
Accurate labor costing directly impacts your business's financial health. Without proper analysis of cost and labor, you risk underpricing your products or services and making uninformed strategic decisions.
Proper labor costing enables:
- Accurate pricing: Setting prices that cover all costs while remaining competitive
- Realistic budgeting: Creating financial plans based on true operational costs
- Informed staffing: Making data-driven decisions about hiring and scheduling
- Regulatory compliance: Meeting tax and labor law requirements
Financial visibility
Detailed labor costing provides transparency that helps you identify profit leaks and understand true project costs. This visibility allows you to pinpoint inefficiencies and determine which products or services generate the most profit.
Financial visibility also helps you evaluate the return on investment for different departments or product lines. This information is invaluable when deciding where to allocate resources for maximum impact.
Fixed vs. Variable Labor Costs
Fixed labor costs remain constant regardless of production volume. These predictable expenses include salaried employees, contracted benefits, and standing management positions.
Variable labor costs fluctuate based on production levels or seasonal demands. These include overtime pay, temporary staff, and production bonuses.
Predictable Expenses
Fixed labor costs provide stability in your financial planning because they remain consistent month to month. Examples include:
- Base salaries for permanent staff
- Management compensation
- Contracted benefit obligations
These expenses form the foundation of your labor budget and represent your minimum operating cost. Understanding your fixed labor costs helps determine your break-even point and minimum revenue requirements.
Fluctuating Labor Needs
Variable labor costs change with business activity and provide flexibility in managing resources. Common examples include:
- Common examples include: – Overtime hours during busy periods
- Seasonal workers
- Production-based bonuses
- Shift differentials for evening work
Effective management of variable labor costs allows you to scale operations in response to demand fluctuations. This flexibility can significantly impact your profitability during seasonal peaks and slowdowns.
The Labor Costing Formula
The basic formula for calculating total labor cost is:
Total Labor Cost = Direct Wages + Payroll Taxes + Benefits + Additional Employer Contributions
This labor cost equation captures both visible and hidden employment costs. Direct wages represent what employees see in their paychecks, while the remaining components represent additional employer expenses.
Book a Demo
See how Synerion's workforce management solutions can streamline your labor costing process and improve financial visibility. Our experts will show you how to capture all costs accurately. Book a Demo Today.
Basic Calculation Steps
To compute labor cost effectively, follow these steps:
- Identify all direct wage payments, including regular pay, overtime, and bonuses
- Calculate employer-paid taxes such as Social Security and Medicare
- Add benefit costs, including health insurance and retirement contributions
- Include other contributions, like training expenses and equipment
- Sum all components to determine your total labor cost
For example, an employee earning $20 per hour ($41,600 annually) might actually cost your business $54,080-$58,240 when including all additional expenses.
Payroll Taxes and Benefits
These often-overlooked components significantly impact your total labor costs:
- Social Security and Medicare: Employers pay 7.65% of wages for FICA taxes
- Unemployment insurance: State and federal programs require employer contributions
- Workers' compensation: Mandatory insurance with rates varying by industry
- Health insurance: A major expense that continues to rise annually
- Paid time off (PTO): Vacation, sick time, and holidays
According to the Bureau of Labor Statistics, benefits typically add 30-40% to base salary costs for most employers. This makes them a critical component when defining labor cost accurately.
How to Calculate Labor Costs
Calculating comprehensive labor costs requires attention to detail and a systematic approach. Start with gross pay calculations and then factor in all additional expenses.
Gross Pay Calculation
For hourly employees, multiply their hourly rate by hours worked, including any overtime at the appropriate rate (typically 1.5x regular pay). For salaried employees, use their annual salary divided by pay periods.
Be sure to include:
- Overtime premiums
- Bonuses and commissions
- Shift differentials
- Holiday pay
For example, a manufacturing employee earning $18/hour who works 45 hours (including 5 overtime hours) would earn $855 in gross pay ($18 × 40 + $27 × 5).
Accounting for Additional Costs
Beyond gross pay, factor in these often-overlooked expenses:
- Onboarding costs: Training and setup for new employees
- Equipment and uniforms: Tools and required clothing
- Workspace allocation: Proportional facility costs
- Administrative overhead: HR time spent on employee management
These additional costs can add 10-20% beyond the standard benefit package. Understanding how to calculate the labor cost completely means including all these components.
Common Pitfalls and Mistakes in Labor Costing
Many businesses underestimate their true labor costs by overlooking key expenses. Avoiding these common mistakes can significantly improve your financial planning and pricing strategies.
Underestimating Hidden Expenses
Watch for these frequently missed costs:
- Onboarding expenses: New employee setup and initial training
- Administrative overhead: HR time spent on employee management
- Technology costs: Software licenses and hardware for each employee
- Compliance expenses: Resources spent maintaining regulatory compliance
- Turnover costs: Recruiting and training replacement employees
True Cost Awareness
The average labor cost of replacing an employee ranges from 50-200% of their annual salary when accounting for all recruitment, training, and productivity losses during transition.
Failing to account for these hidden expenses leads to artificially low labor cost estimates and potentially unprofitable pricing decisions.
How to Use Labor Cost Data for Pricing
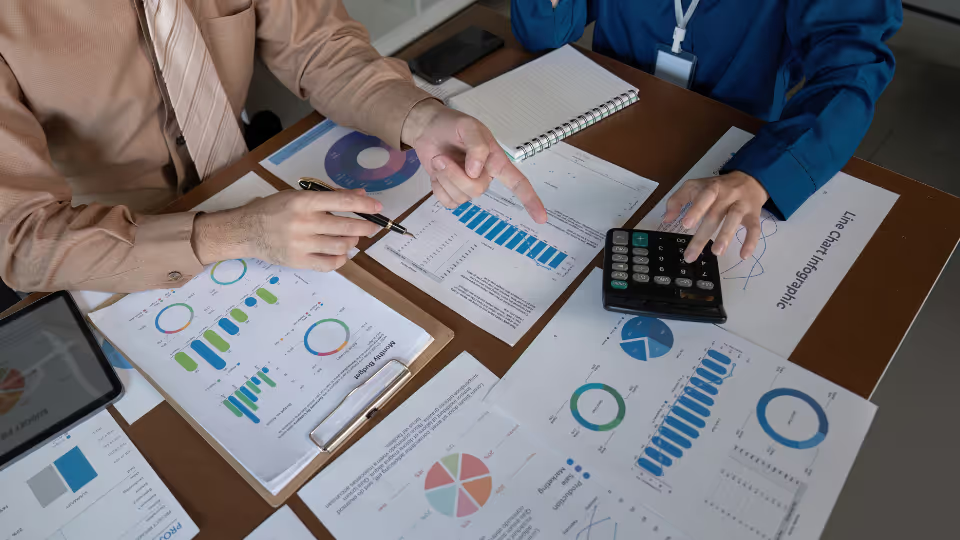
Once you've calculated accurate labor costs, you can develop pricing strategies that ensure profitability while remaining competitive in your market.
Aligning Costs with Markup Strategies
Different industries use varying approaches to labor price markup:
- Manufacturing: Typically applies a 2-3x multiplier to direct labor costs
- Service businesses: Often use a 2-4x multiplier depending on skill level required
- Construction: Commonly uses a 1.5-2.5x multiplier on labor
Your specific markup should account for your indirect costs, desired profit margin, and competitive landscape. The labor fee you charge customers must cover all these components while remaining marketable.
Maintaining Healthy Profit Margins
To maintain healthy margins as labor costs change:
- Conduct quarterly reviews of labor costs against pricing
- Adjust prices proactively when costs increase significantly
- Consider efficiency improvements before price increases
- Track labor percentage relative to revenue
Understanding how to calculate labor cost percentage helps you monitor this critical metric. The formula is simple: (Total Labor Cost ÷ Total Revenue) × 100.
Real-World Industry Examples of Labor Costing
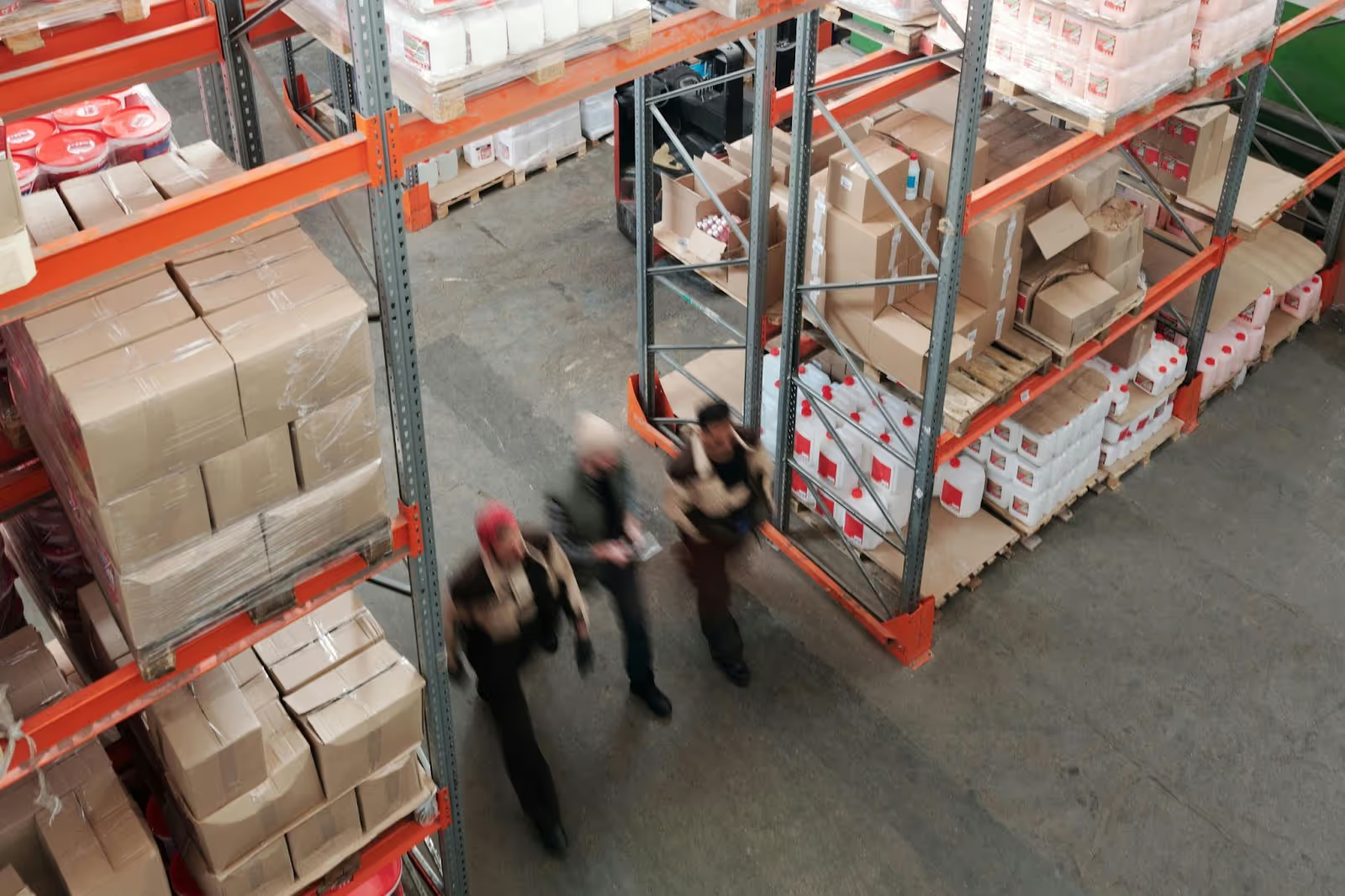
Different industries face unique labor costing challenges and opportunities. Understanding industry-specific approaches can help you implement best practices in your business.
Manufacturing businesses typically track labor costs by production line, shift, and product category. This detailed tracking enables:
- Accurate product pricing based on true production costs
- Identification of efficiency opportunities between shifts
- Make-or-buy decisions for components based on internal costs
- Implementation of labor efficiency metrics like units per labor hour
The direct labor cost formula in manufacturing often includes both the base wage and a portion of supervision and quality control costs. This provides a more accurate picture of what it truly costs to produce each unit.
Advanced Strategies to Optimize Labor Costs
Beyond basic calculation, implementing advanced labor management strategies can help optimize costs while maintaining quality and employee satisfaction.
Workforce Management Solutions
Modern workforce management tools provide significant advantages:
- Automated scheduling: Creates optimal schedules based on demand forecasts
- Time and attendance tracking: Eliminates time theft and simplifies payroll
- Labor forecasting: Predicts staffing needs based on historical patterns
- Mobile accessibility: Allows employees to clock in/out from anywhere
These solutions typically reduce labor costs through the prevention of unnecessary overtime and improved scheduling efficiency. They also provide accurate data for labor cost percentage formula calculations.
Employee Engagement Initiatives
Investing in employee engagement directly impacts labor costs through:
- Reduced turnover: Engaged employees are less likely to leave
- Lower absenteeism: Engaged employees take fewer unscheduled absences
- Higher productivity: Engaged employees accomplish more in less time
Even modest improvements in engagement can yield significant cost savings while creating a more positive workplace culture. This approach addresses labor costs that often remain hidden in traditional accounting.
Technology & Tools for Effective Labor Costing
Implementing the right technology solutions can dramatically improve your labor costing accuracy while reducing the administrative burden...
Automated Time Tracking Systems
Modern time tracking solutions offer significant advantages over manual systems:
- Biometric verification: Prevents buddy punching through fingerprint or facial recognition
- Mobile capabilities: Allows remote workers to clock in/out accurately
- Job coding: Captures time spent on specific projects or tasks
- Rule enforcement: Automatically applies company policies for breaks and overtime
These systems typically pay for themselves quickly through improved accuracy and reduced administrative time. They also provide the data needed to calculate total labor cost across departments or projects.
Real-Time Analytics Dashboards
Advanced labor costing systems provide real-time visibility through:
- Customizable dashboards: Display key metrics relevant to different managers
- Trend analysis: Identifies patterns in costs over time
- Department comparisons: Highlights variations in efficiency across teams
- Variance alerts: Notifies managers when costs exceed budgeted amounts
This real-time visibility allows for proactive management rather than reactive responses to problems after they occur. You can monitor average labor cost metrics and identify outliers requiring attention.
Elevate Your Workforce Management with Synerion
Effective labor costing forms the foundation of sound business decision-making. By accurately tracking all components of your labor expenses, you gain the insights needed to price profitably and allocate resources efficiently.
Synerion's workforce management solutions provide the tools you need to master labor costing without the enterprise-level price tag. Our solutions integrate with your existing systems while providing advanced features typically found only in much more expensive platforms.
Our in-house implementation team ensures your system captures all the labor cost components specific to your business. Request a demo today to see how Synerion can transform your approach to workforce management.
Frequently Asked Questions About Labor Costing
How Do Labor Costing Systems Integrate with Existing Payroll Software?
Modern labor costing solutions connect seamlessly with your current payroll systems through standard APIs and pre-built integrations, eliminating double data entry while providing comprehensive cost analysis.
What Industries Benefit Most from Advanced Labor Costing Methods?
Manufacturing, healthcare, retail, and hospitality operations gain the most value due to their complex workforce structures, multiple shifts, and need to allocate costs to specific products or departments.
How Can Small Businesses Implement Effective Labor Costing?
Small businesses should start with spreadsheet tracking of all labor components and gradually implement specialized software as they grow, focusing first on accurate time tracking and classification of costs.
What Is the Difference Between Labor Costing and Labor Pricing?
Labor costing involves calculating all expenses associated with employing workers, while labor pricing refers to how much you charge clients for labor in service-based businesses, typically including a markup for overhead and profit.
How Often Should Businesses Review Their Labor Costing Methods?
Conduct quarterly reviews to identify short-term trends and perform a comprehensive annual analysis to assess the impact of benefit changes, wage adjustments, and market conditions on your overall labor costs.